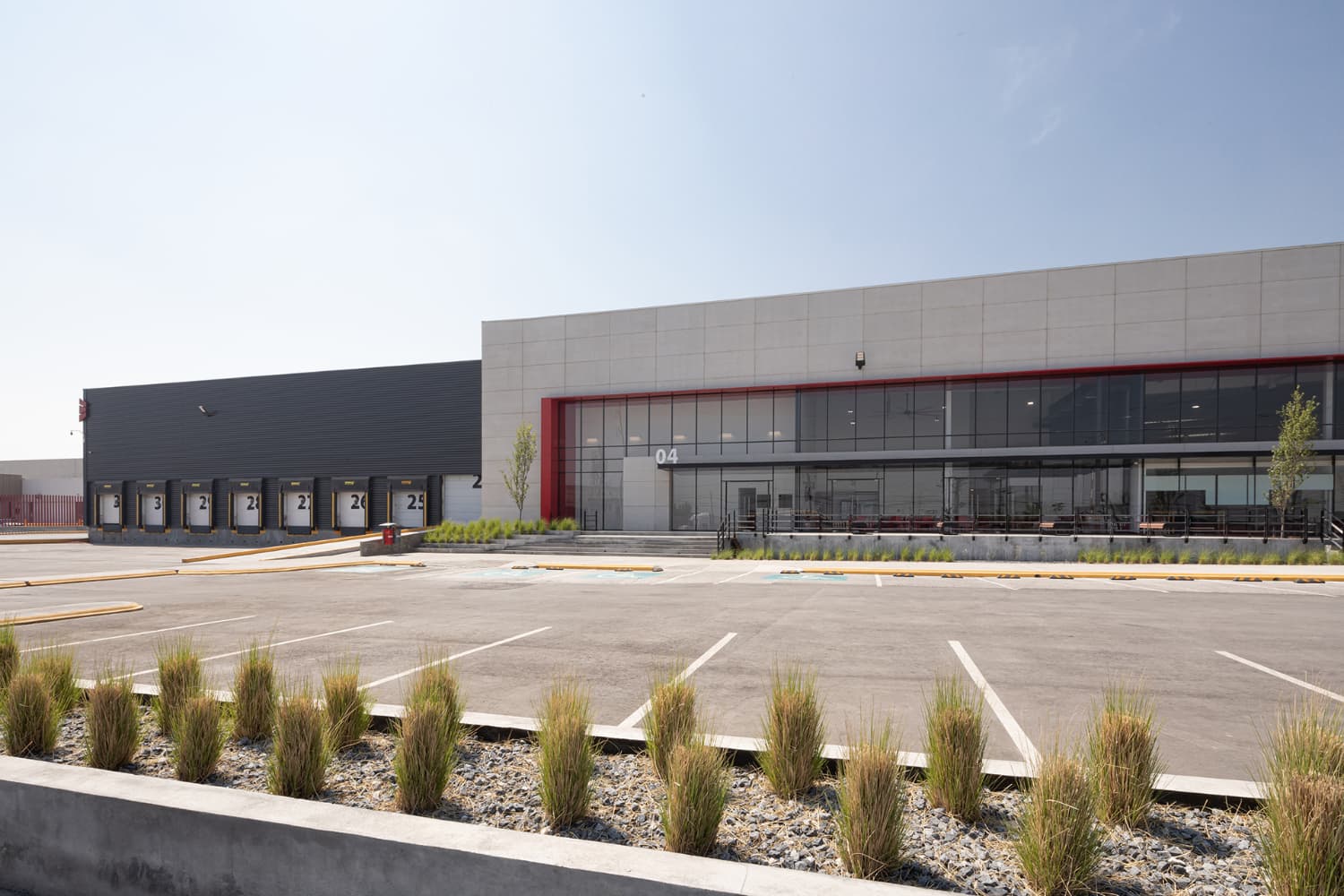
General description
ProximityParks Monterrey Centro
ProximityParks Monterrey Centro is part of the portfolio of the developer ProximityParks, which is based on meeting the characteristics of urbanization, consumer demand and sustainability.
The project is located in downtown Monterrey, in an existing building where a warehouse with three guardhouses, office area and a common area for users was built.
In addition to the benefits of its location, the project implemented strategies to reduce water, waste, and electricity consumption. In addition to the design, the project implemented consumption monitoring strategies to ensure that good practices continue during operation and achieve the expected reduction.
All of these strategies together enabled the company to obtain gold level certification.
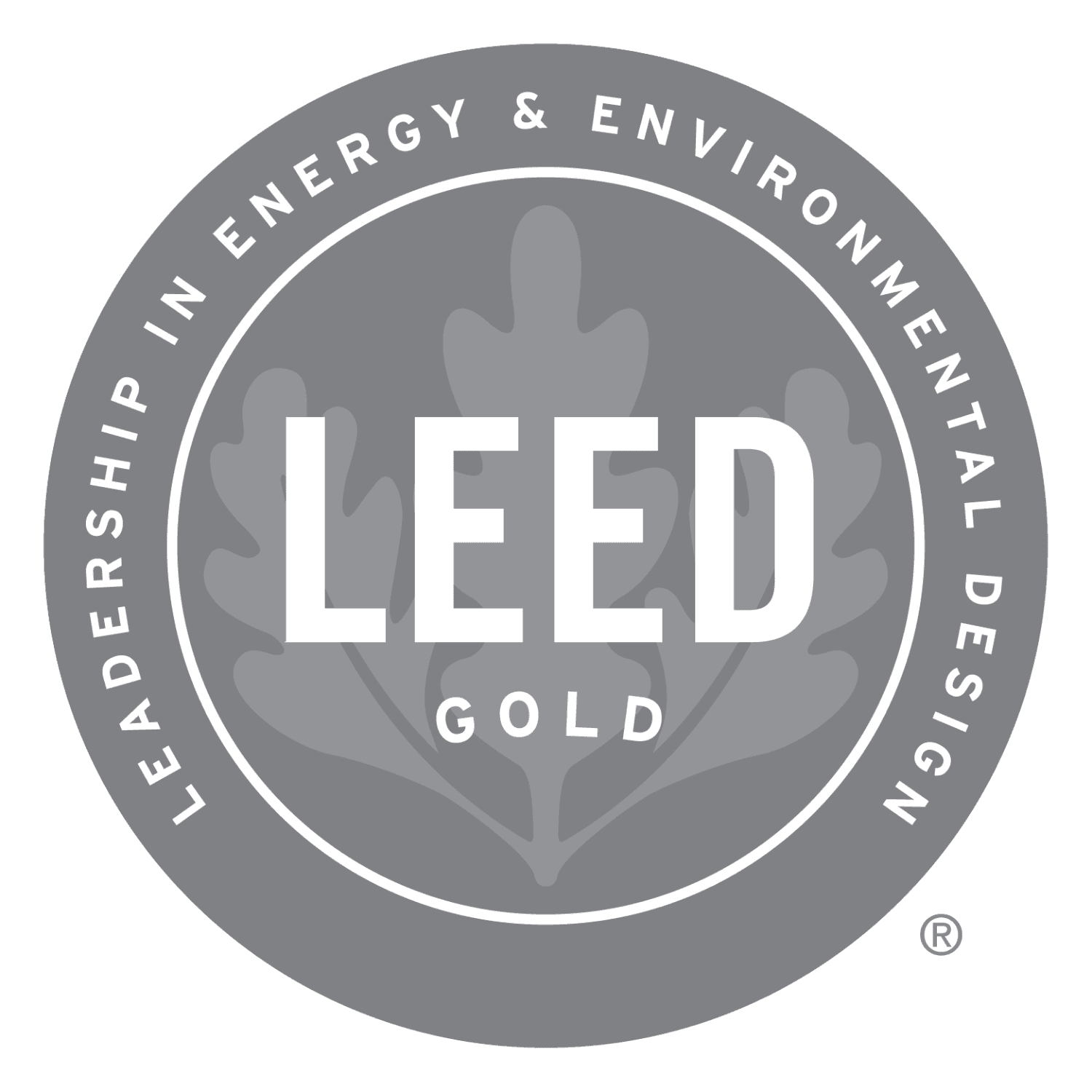
Company
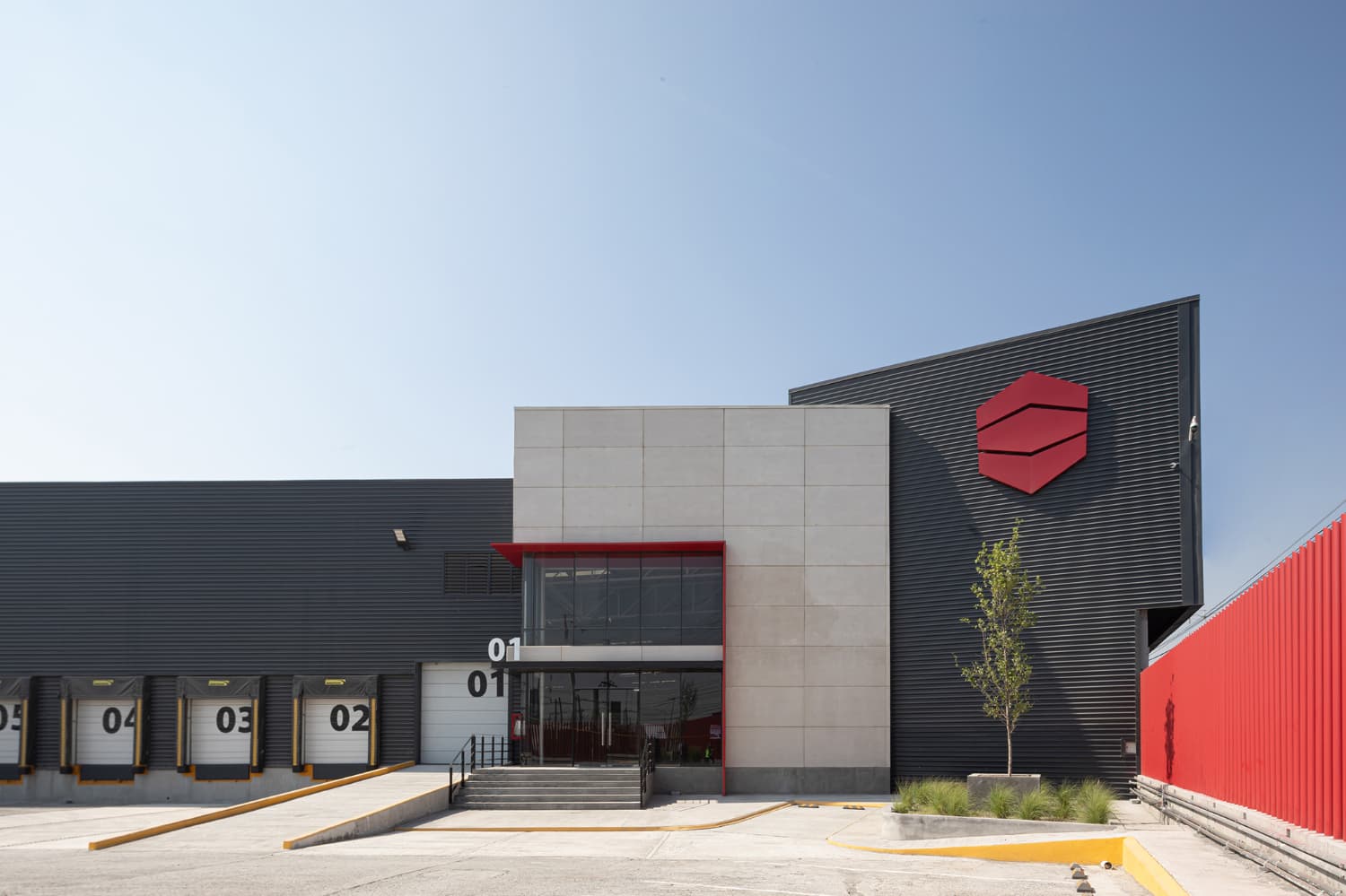
ProximityParks
ProximityParks was founded in 2017 and became the first "last mile" industrial real estate investment company dedicated exclusively to Latin America.
Project
Sustainable Design
From the beginning, it was planned to locate the project in a densely developed and accessible place in order to reduce transportation.
Likewise, an existing warehouse was acquired in order to reuse approximately 58.86% of the existing materials, thus reducing the extraction and transfer of raw materials. First, electricity consumption was reduced through the use of efficient lighting and air conditioning equipment, and for the remaining consumption, 436 solar panels were installed.
In terms of comfort and indoor air quality, louvers were installed on facades to incorporate natural ventilation, and CO₂ sensors were located to identify inadequate levels of air quality.
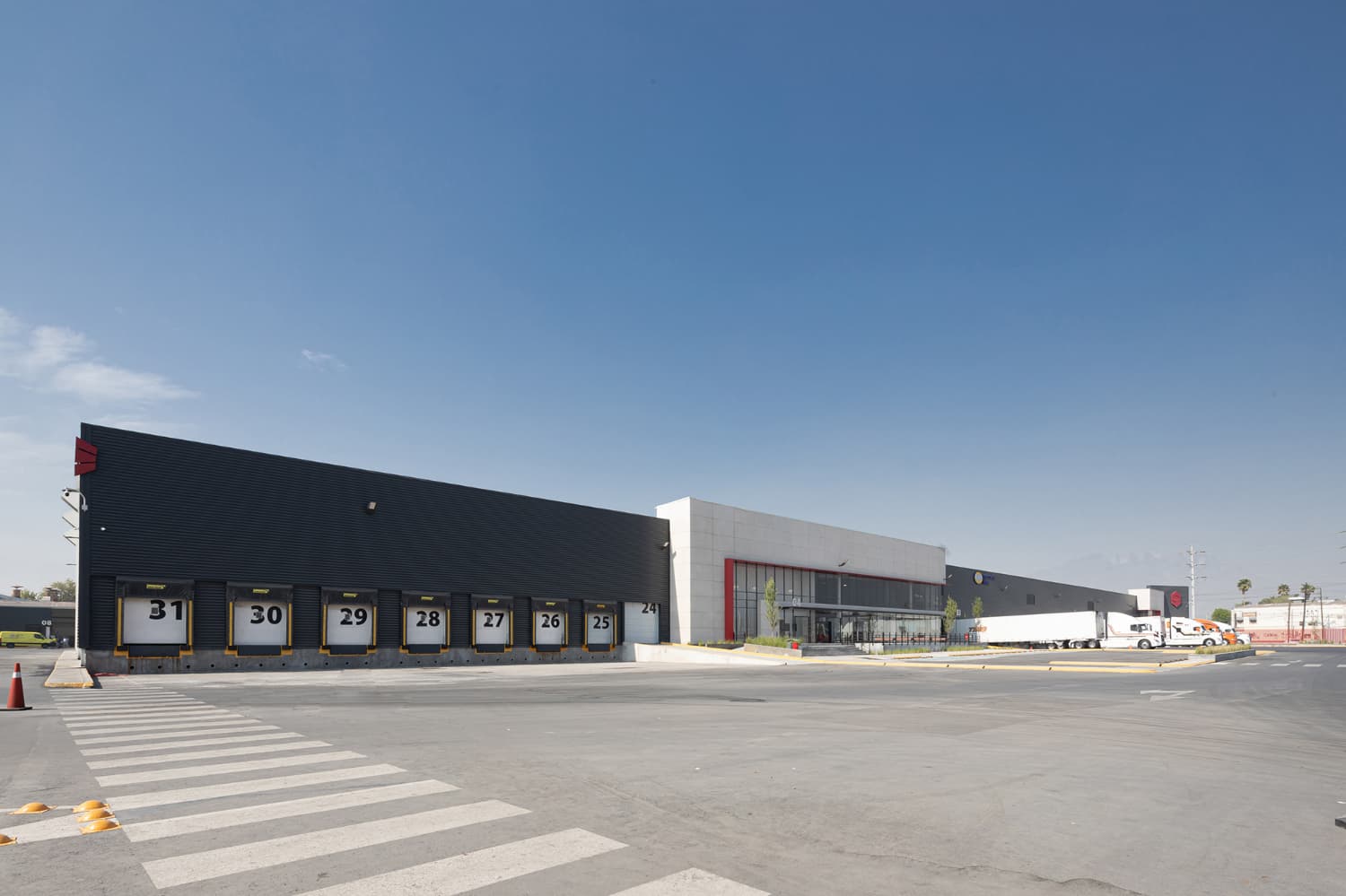
Challenges
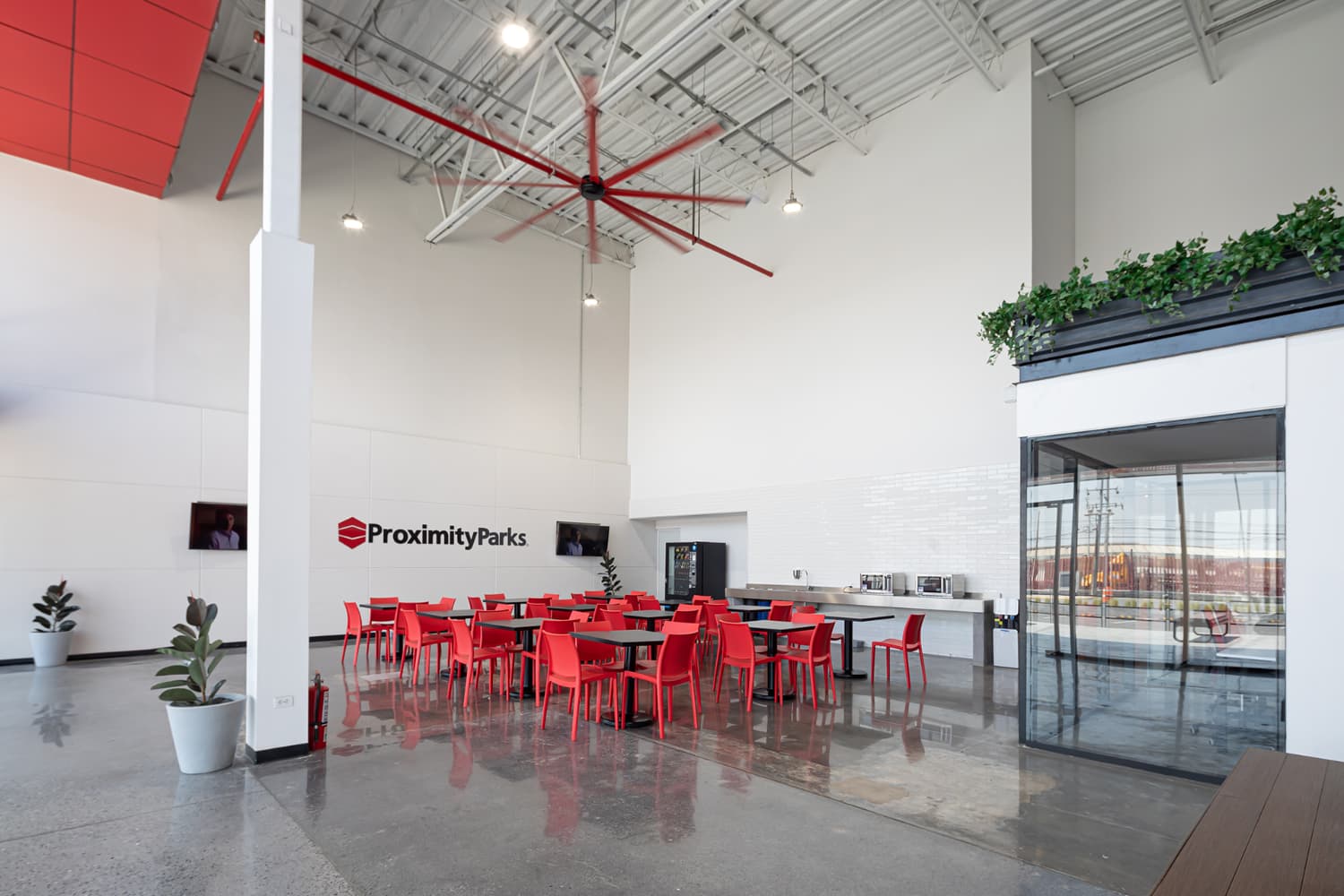
A sustainable idea
It was the first project for ProximityParks to seek LEED certification.
Solution
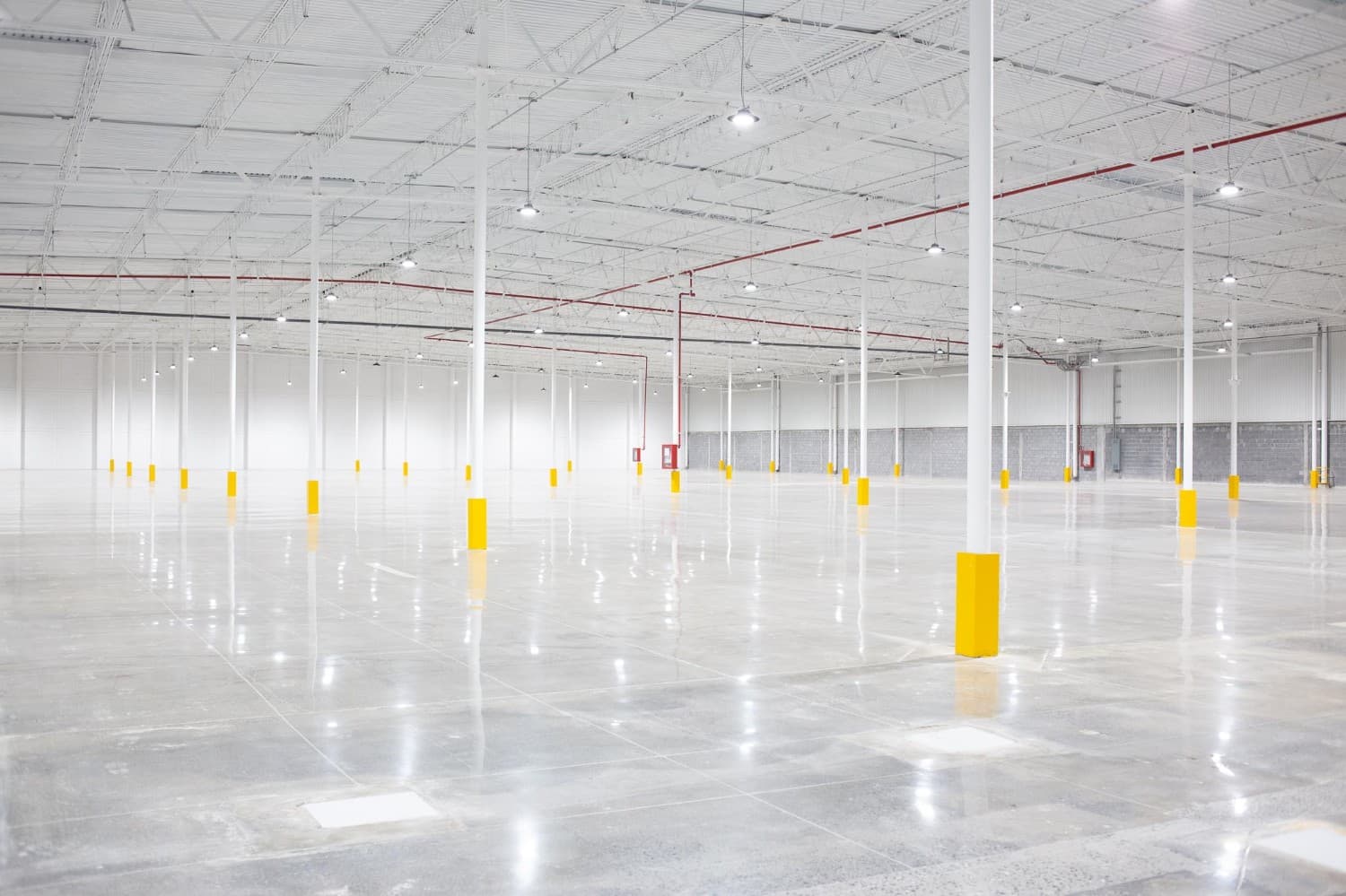
Volume Model
The continuous training of the team and contractors was essential to ensure a high level of quality and safety in the development of this project. In this case, the first project was a success, which allowed the implementation of the "Volume" prototype.
This positive experience led the company to decide to certify the rest of the industrial warehouses under this prototype, which implied additional training and an investment in resources to adapt the existing industrial warehouses to this new methodology.
However, the company felt that this decision was necessary to standardize and optimize processes in all its facilities.